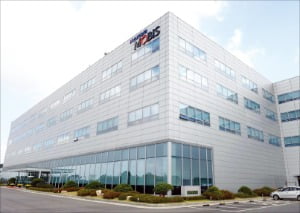
1990년대부터 자동차 분야에서는 3D프린팅을 ‘쾌속 조형(RP·Rapid Prototype)’으로 불리는 디자인 검증 중심으로 활용했다. 하지만 최근 몇 년간 3D프린팅 생산기술 투자, 완제품 생산을 위한 연구개발 확대 등을 바탕으로 많은 자동차 회사가 3D프린팅으로 완제품(부품)을 개발하는 데 주력하고 있다. BMW, 폭스바겐, 포드, 제너럴모터스(GM), 현대자동차 등이 3D프린팅 특화 조직을 운영하고 있다. 3D프린팅에 관한 연구개발을 늘리고 관련 제품을 시장에 선보이기도 했다. 이는 3D프린팅의 장점을 극대화할 수 있는 ‘적층제조를 위한 특화 설계(DfAM·Design for Additive Manufacturing)’가 등장한 데 따른 것이다.
DfAM은 공학 시뮬레이션을 기반으로 한 3D프린팅 특화 설계 방법이다. 기존 설계 또는 제조의 한계점을 극복할 수 있다. 여러 개 부품으로 구성된 모듈을 한 개의 부품으로 제작할 수도, 위상 최적화를 활용해 기존과 동일한 성능을 내면서 가벼운 제품을 만들 수도 있다. 3D프린팅으로 특정 성능과 중량을 목표로 하는 부품을 제작하려고 할 때는 시뮬레이션 소프트웨어(SW)의 도움을 받으면 된다. 목표 값과 필요한 3D프린팅 기법 등을 포함한 3D 모델링이 가능하다.
과학기술정보통신부가 주최한 ‘2022년 3D프린팅 활용 우수사례 경진대회’에서 1위인 장관상을 받은 현대모비스의 ‘3D프린팅을 이용한 DfAM 적용 e-코너모듈 부품 개발’이 이런 사례다. 현대모비스는 해당 사례에서 제동, 조향, 섀시(뼈대) 등 다양한 성능 조건과 여러 주행 환경을 동시에 고려해 부품을 설계했다. 위상 최적화를 포함한 DfAM으로 여러 성능과 제약 조건을 동시에 만족하면서도 설계 기간을 단축하고 부품 중량을 20% 이상 낮춘 제품을 선보였다.
모빌리티 시장은 내연기관 자동차에서 전기자동차 시장으로, 그리고 목적기반모빌리티(PBV)와 미래항공모빌리티(AAM)로 확장되고 있다. 새로운 패러다임으로 바뀌는 모빌리티 시장의 패권을 주도하기 위해선 혁신적인 변화가 필요하다. DfAM과 3D프린팅이 과거에는 보지 못했던 고성능 및 경량화 부품을 개발하고, 혁신을 이끌어갈 원동력이 될 것으로 기대해 본다.
현대모비스 기술연구소