종업원 30명의 중소업체지만 5년새 시설 4배 이상 늘려
구로·성남 등에 시험연구실
초음파 엑스레이 장비 등 첨단 장비 모두 갖춰
신속 정확한 검사가 강점…의뢰 들어오면 주말도 근무
"한국의 SGS 되는 게 꿈"
[ 김낙훈 기자 ]

사람이 아프면 병원으로 달려간다. 기업이 자사 제품에 불량이 생기면 찾아가는 곳이 있다. 서울 구로동에 있는 아프로R&D(사장 김형태·47)라는 중소기업이다. 왜 현대 삼성 LG 등 내로라하는 대기업이 종업원 30명에 불과한 업체의 문을 두드리는 것일까.
서울 구로디지털밸리에 있는 아프로R&D에 들어서면 초음파 장비, 엑스레이 장비, 컴퓨터단층촬영(CT) 장비 등이 놓여 있다. 얼핏 보면 병원에 온 듯하다. 하지만 이곳은 각종 전기·전자·자동차 부품과 소재의 문제 여부를 검사하는 곳이다.
전자제품이 고장 나면 회로나 부품을 검사해야 고칠 수 있다. 예컨대 인쇄회로기판(PCB)에 붙어 있는 전자부품이 제 기능을 못할 때 다리처럼 생긴 리드와 PCB 회로를 연결하는 접착제(무연솔더)가 제대로 발라지지 刻티?适? 혹은 접착제와 리드 사이에 미세한 금(크랙)이 생겨서인지 등을 찾아내야 한다.
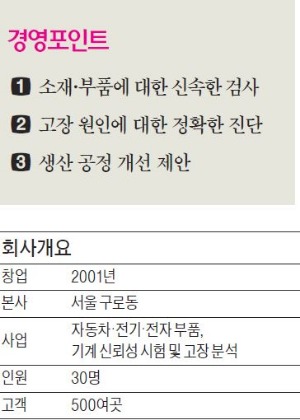
때로는 파괴검사도 실시한다. 샌드위치의 내용물을 정확히 파악하기 위해 반으로 잘라 단면을 들여다보면 되듯 연마제로 부품 옆면을 지속적으로 갈아 단면이 나오면 정밀 현미경으로 보는 것이다. 이를 위해 이 회사는 20만배율의 주사전자현미경(SEM)도 보유하고 있다.
이 회사가 하는 일은 불량 여부를 검사하는 것에서 그치지 않는다. ‘역설계·분해공법’을 이용해 불량 원인을 찾고 때로는 생산공정에서 원천적으로 불량을 막는 방안을 제안하기도 한다. 개선된 제품에 대한 내구성 시험(온도 습도 진동 등)을 통해 제품 수명을 예측하기도 한다.
이처럼 자동차나 전자제품 휴대폰 등에 불량이 생기면 원인을 찾고 개선 방안을 종합 제공해주는 곳이 바로 아프로R&D다. ‘기업들의 종합병원’인 셈이다.
이 회사는 최근 5년 새 연구시험실 공간을 4배 이상 늘렸다. 서울 구로, 경기 성남·김포에 시험실을 두고 있는데 올해도 시설을 꾸준히 확장하고 있다. 이 회사가 입주한 지식산업센터는 대개 230㎡ 안팎 크기로 한 개의 방이 구성되는데 5년 전만 해도 겨우 방 2개를 썼다. 이를 9개로 확충했고 올해 더 확장할 예정이다. 자체 연구원도 15명에서 30명으로 2배 늘렸고 올해 5명을 추가로 충원할 계획이다. 외부전문위원 30여명과도 협업하고 있다. 이같이 꾸준히 성장하는 까닭은 무엇일까.
첫째, 신뢰할 수 있는 검사다. 초음파, 엑스레이, CT 장비가 있다고 다 정확한 검사를 하는 것은 아니다. 병원에서도 똑같이 찍은 엑스레이 사진을 놓고 미세한 초기 암을 찾아내기도 하고 놓치기도 한다. 마찬가지다. 첨단장비로 금속을 검사해도 판독하는 것은 결국 사람의 몫이다. 이 회사는 창업한 이후 14년 동안 오로지 이 일만을 하며 경험을 축적해왔다.
창업자인 김형태 사장은 성균관대 금속공학과를 졸업하고 동 대학원에서 석·박사 학위를 받았다. 그는 “국내 제조업이 한 단계 도약하려면 무엇보다 부품·소재의 신뢰성이 높아져야 하고 이를 위해선 부품에 대한 정확한 검사와 문제 진단, 개선 방안 마련이 중요하다고 생각했다”고 창업 이유를 밝혔다.
그는 수천 건의 시험검사를 해오며 △전기·전자부품의 고장 분석 △항공·철도 소재의 파손 원인 분석 △자동차 부품의 무연솔더링(납을 제거한 땜질) 접합부 신뢰성 향상 등의 성과를 거뒀다. 김 사장은 “특히 무연솔더링 분야의 불량 여부 검사와 개선 방안에 대해 수많은 노하우를 축적해왔다”고 설명했다.
명의가 되려면 많은 수술 경험이 필요하듯 김 사장은 수많은 고객의 제품을 분석하고 그 결과를 통해 신뢰를 쌓아왔다. 예컨대 어떤 부품의 경우 대기업과 공공기관에서 여러 차례 검사를 통해 문제가 없 鳴?판단한 것을 아프로R&D에서 문제점을 정확히 집어낸 적이 있다. 이 대기업은 아프로R&D의 단골 고객이 됐다. 그는 “우리 회사의 고객이 5년 새 300여곳에서 500여곳으로 늘어난 것도 이런 믿음 덕분”이라고 설명했다. 국제공인시험기관(KOLAS)의 인정을 받은 것을 비롯해 항공·철도사고조사위원회의 시험분석실 운영 등을 통해 국가나 공공 부문으로부터 신뢰도 얻었다.
이 회사의 고객은 국토해양부 한국수력원자력 등 국가 및 공공기관, 현대자동차 삼성전자 대한항공 만도 휴맥스 등 국내 주요기업, 보쉬 발레오 덴소 콘티넨탈 알프스 등 외국 기업 등이다.
둘째, 신속한 검사와 리포트 작성이다. 민간기업은 급하게 검사를 의뢰하는 경우가 많다. 이 회사의 연구원들은 언제 어떤 요구가 들어와도 성실하게 검사한다. 금요일 퇴근시간이 임박해 고객이 공공기관이나 대학에 검사를 의뢰하면 대개 월요일 이후에 검사를 시작하지만 이 회사는 주말에도 철저하게 검사해 월요일 오전에 고객 책상에 리포트를 갖다놓는다.
셋째, 끊임없는 투자다. 김 사장은 사업을 하면서 초창기에 많은 어려움을 겪었다. 정확한 시험검사를 위해선 고가의 장비를 꾸준히 마련해야 했다. 초음파, 엑스레이, CT 장비 등은 병원에서 쓰이는 것보다 정밀도가 높고 비싸다. 마이크로미터 단위의 미세한 크랙을 잡아내야 하기 때문이다. 중소기업이 이를 장만하는 것은 쉬운 일이 아니다. 이들 장비뿐 아니라 주사전자현미경 등 수많은 장비의 가격이 대당 수억원에 이르는 경우가 비일비재하다.
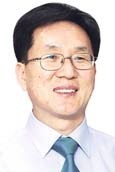
김 사장은 “주문이 꾸준히 늘면서 이제는 사업이 안정 궤도에 올라섰다”며 “특히 부품 불량 판독과 원인 분석에 이어 개선 방안까지 제안해주면 고객이 무척 기뻐한다”고 덧붙였다. 물론 모든 공정의 개선 방안을 제안할 수 있는 것은 아니다. 하지만 이 회사가 제안한 방안은 신뢰할 만하다고 평가받는 단계에까지 올라섰다고 김 사장은 설명했다. 그는 “이런 측면에서 부품·소재산업 발전의 작은 부분을 맡고 있다는 자부심을 느낀다”고 말했다.
그의 꿈은 ‘한국의 SGS’가 되는 일이다. 김 사장은 “SGS는 세계적인 시험검사기관으로 매우 높은 신뢰성을 인정받고 있다”며 “몇몇 분야의 시험검사에서 SGS만큼 인정받는 기업을 일궈내겠다”고 강조했다. 그는 “독일이 금속을 비롯한 소재산업에서 세계 정상을 달리는 것은 끊임없는 기술개발과 더불어 철저한 검사와 이를 토대로 한 지속적인 개선이 이뤄지고 있기 때문”이라며 “한국의 부품·소재 분야가 독일과 겨룰 수 있도록 힘을 쏟겠다”고 덧붙였다.
김낙훈 중소기업전문기자 nhk@hankyung.com
[한 ? 구독신청] [기사구매] [모바일앱] ⓒ '성공을 부르는 습관' 한국경제신문, 무단 전재 및 재배포 금지