신형기 B787-9 부품 제조 한창…이달 말 국내 첫선
(부산=연합뉴스) 윤보람 기자 = 김해국제공항 인근 대한항공[003490] 부산테크센터의 복합재2공장 안에 들어서자 천막 문으로 외부와 차단된 공간이 보였다.
문이 열리고 모습을 드러낸 작업장에서는 항공기 동체 뒷부분인 애프터 보디(After Body)를 복합재로 겹겹이 쌓는 '레이업' 공정이 한창이었다.
내부를 좀 더 살펴보고 싶었지만 야속하게도 문은 1∼2분 만에 닫혔다. 외부인이 무방비 상태로 장시간 머무르면 복합재 성분이 오염될 우려가 있어서다.

지난 17일 찾은 대한항공 부산테크센터는 차세대 항공기 B787-9에 들어가는 부품을 제조하느라 분주했다.
'드림라이너'(꿈의 항공기)라는 이름이 붙은 B787은 보잉사가 주력으로 삼는 기종이다.
기체의 50% 이상을 탄소 복합소재로 만들어 무게를 획기적으로 줄이는 동시에 강도는 높인 것이 특징이다.
연료 효율이 다른 기종보다 20%가량 높고 가스 배출이 적어 친환경적이기도 하다.
한층 커진 창문과 높아진 천장, 향상된 기내 습도는 승객에게 매력적인 요소다.
B787 시리즈 중 최신 모델인 B787-9는 직전 모델인 B787-8보다 효율성을 높였다. 최대 운항 거리는 약 1만5천750㎞로 550㎞ 길어졌고 장착 좌석은 250∼290석으로 30여석 늘었다.
대한항공은 B787-9 1호기를 국내 최초로 이달 말 도입하기 시작해 총 10대를 차례로 들여올 예정이다.
이처럼 최첨단 항공기 제작 기술이 집약된 B787-9 항공기에는 대한항공이 만든 핵심 부품이 포함돼있다.
대한항공은 2004년부터 B787 제작·설계 사업에 참여해 날개 구조물인 레이키드 윙팁(Raked Wing Tip), 플랩 서포트 페어링(Flap Support Fairing), 애프터 보디 등 5가지 부품을 부산테크센터에서 제작하고 있다.
특히 곡선 모양인 레이키드 윙팁은 공기 저항을 줄이는 데 필수적인 구조물로 보잉사로부터 높은 기술 수준을 인정받았다.
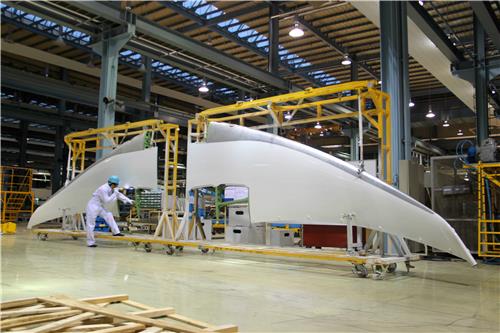
최첨단 기술력을 갖추기까지는 오랜 시간과 많은 노력이 필요했다.
대한항공은 1986년부터 B747-400 항공기 날개 구조물을 제작해 수백 대분의 구조물을 납품하면서 관련 기술과 경험을 축적했다.
B787 국제공동개발사업에 참여하려고 과감한 설비 투자를 했으며 전문 인력은 20∼30년 경력의 '베테랑'들로 채웠다.
대한항공 항공우주사업본부의 이재춘 사업계획팀장은 "국제공동개발사업에 참여하는 업체는 개발·설계·생산·시험·인증 등 모든 과정을 직접 수행한다"며 "구조물을 항공사에 인도한 뒤 유지·보수까지 책임질 만큼 기술력이 뛰어나야 한다"고 설명했다.
1976년 세워진 대한항공 항공우주사업본부는 국내 최초로 500MD 헬기를 생산하는 등 40년 넘게 항공기 제조 산업을 이끌어왔다.
부산테크센터는 21만평 규모에 2만5천여종이 넘는 각종 장비와 3천여명의 인력을 갖췄으며 민항기뿐 아니라 군용기, 무인기의 생산·정비도 맡는다.
특히 본부는 무인기 사업에 공을 들이고 있다. 보잉사와 양해각서(MOU)를 체결해 500MD 무인화 작업을 진행 중이며 연내 완료를 목표로 공격용 무인헬기 개발도 추진하고 있다.
본부는 연평균 20% 성장을 지속하며 2015년 매출 1조원을 처음 돌파했다. 지난해에는 1조269억원을 기록해 대한항공 전체 매출의 10%를 차지했다.
이재춘 사업계획팀장은 "사업화 가능성이 큰 무인기 성능개량 부문을 확대해 2020년에는 2조원, 2025년에는 3조원의 매출을 달성하는 것이 목표"라고 말했다.
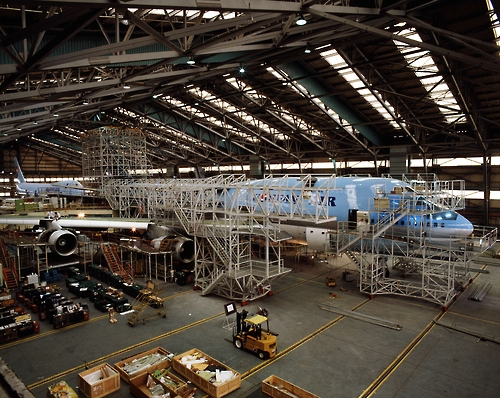
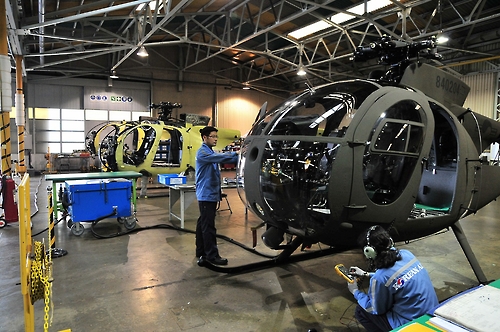
bryoon@yna.co.kr
(끝)
<저작권자(c) 연합뉴스, 무단 전재-재배포 금지>