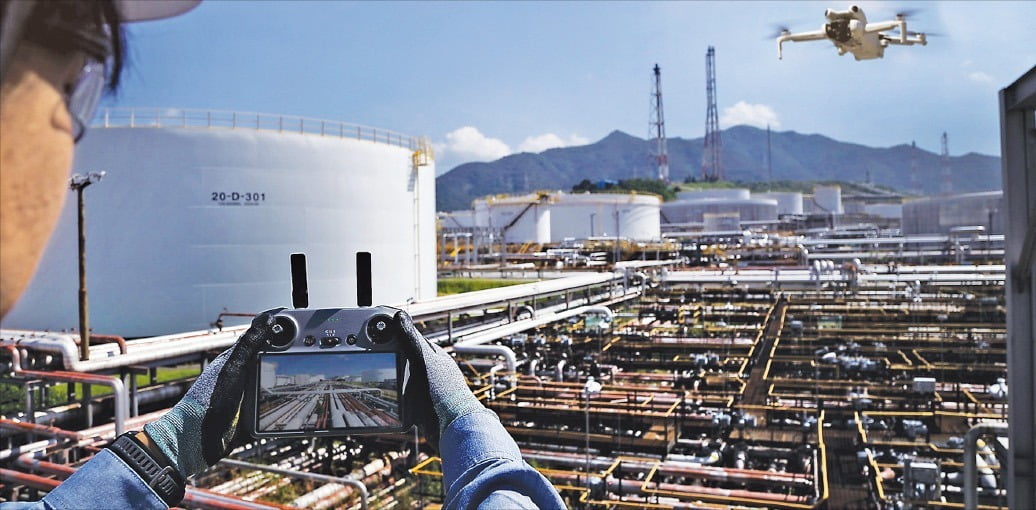
GS칼텍스 전남 여수공장엔 원유를 끓이기 위한 84개의 가열로와 이 안에 든 1665개의 버너가 있다. 가열로와 버너를 다루기 위해 투입되는 직원은 약 600명. 이들이 각자의 경험과 눈으로 가열로 안의 불꽃 상태를 조절하다 보니 불꽃의 편차가 발생하거나 불필요한 연료를 쓰는 일이 많았다.
비효율을 줄이기 위해 GS칼텍스는 수년간 노력했고, 결국 가열로 시스템을 디지털로 전환하는 데 성공했다. 실시간 가열로 모니터링뿐 아니라 버너 상태를 그래프로 나타내기 시작한 것. GS칼텍스 관계자는 “디지털 전환을 통해 연 23억원의 연료비를 절감했고 온실가스 배출량은 1만t이나 줄었다”고 강조했다.
GS칼텍스가 여수공장의 전 업무 영역을 디지털화하는 데 성공했다. 사람의 힘이 절대적이었던 공정 최적화와 설비 통합 관리, 안전·환경 업무 등에 디지털 기술을 입힌 것이다. GS칼텍스는 이를 통해 2030년까지 총 1000억원의 비용을 절감할 계획이다.
○허세홍 사장 “경쟁력은 DX서 나와”
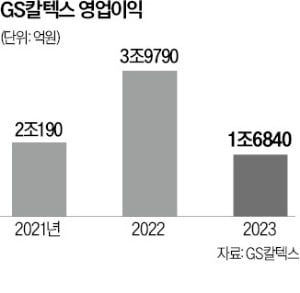
회사 측은 이런 비용을 아끼기 위해 공장을 한눈에 확인할 수 있는 ‘설비·관리 통합플랫폼’을 우선 도입했다. 회전기계 이상을 감지하고, 배관 두께를 측정해 인공지능(AI)으로 분석하는 모델 등을 적용했다. 주요 회전기계의 진동 정도를 분석해 조기에 이상을 감지할 수 있다. 또 엑스레이로 배관을 촬영해 AI가 이를 분석한 뒤 이상 여부를 판단할 수 있게 했다. 가열로의 디지털화도 마찬가지다. 지난해 버너 사용에 들어간 연료만 1조1000억원어치였는데, 디지털화를 통해 쓸데없는 연료 낭비가 상당히 줄었다는 설명이다.
○생산 계획도 디지털화
생산 계획 역시 상당 부분을 디지털화했다. 정유업은 유가 변동, 환율 등 외부 변수가 많아 체계화된 생산 계획이 필요하다. GS칼텍스는 원유 등 가격 전망, 구매, 물류, 판매, 시장 예측 등 수많은 데이터를 취합하고 이를 정량화해 생산 계획을 수립하고 있다.엔지니어 등 현업 근로자에게 디지털 기술을 교육하고 있는 것도 한 특징이다. GS칼텍스 관계자는 “정보기술(IT) 부서에 모든 걸 맡기면 현장에서 적용하기 어렵다”며 “여수공장이 현장에서 가장 필요로 하는 DX를 도입할 수 있었던 이유”라고 설명했다.
GS칼텍스가 석유화학까지 밸류체인을 확대하며 DX의 활용처는 더 넓어지고 있다. 이 회사가 2조7000억원을 투자한 올레핀복합분해설비(MFC) 설비는 국내 정유사 최초의 ‘정유·석유화학 통합 공장(COTC)’이다. DX를 통해 제품 수율(완성품 중 양품 비율)과 원자재 투입 효율성 등을 최적화하고 있다.
GS칼텍스는 AI CCTV와 드론도 공장에서 활용하고 있다. CCTV 855대 가운데 164대인 AI CCTV는 외부인이 침입하거나 공장에 불이 나는 등 사고가 발생하면 직원에게 알림을 준다. 공장 외부 및 내부를 검사하기 위한 드론도 운영하고 있다.
여수=김형규 기자 khk@hankyung.com