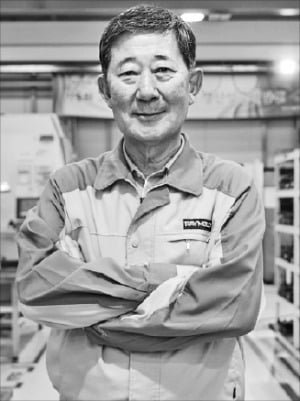
최근 자동차 내장재와 TV 등 가전제품 표면에 광택을 내며 얇고 미려한 곡선의 디자인을 구현하려는 업계 시도가 늘고 있다. 제품 표면에 광택을 내려면 도장 작업이 따른다. 이는 환경오염을 수반해 탄소 배출을 줄이려는 자동차·가전업계의 고민이 컸다. 제품의 대량 생산에 필요한 ‘틀’을 납품하는 금형업계 역시 크나큰 숙제를 안고 있었다.
금형업체 레이몰드는 스프레이 분사 등 도장 작업 없이도 플라스틱에 고광택을 낼 수 있는 ‘무도장 친환경 금형 기술’과 ‘초정밀 미세 가공 기술’을 선보여 전 세계 자동차·가전업체가 찾는 기업이 됐다. 레이몰드를 설립한 하광운 대표는 국내 금형 기술 개발 공로를 인정받아 19일 열리는 ‘제25회 금형의 날’ 행사에서 ‘올해의 금형인’으로 선정된다.
초정밀 기술개발 등 ‘K금형’ 선도
하 대표는 45년간 금형을 설계해온 기능인이자 경영자다. 37년간 레이몰드를 이끌어왔다. 이 회사는 1981년 비디오·오디오 버튼을 만들 때 쓰이는 금형 기술 ‘전주금형코어’를 국내 최초로 개발하고 1999년 액정표시장치(LCD) 등 디스플레이 액정 성형에 쓰이는 ‘무인쇄·초박형 도광판’을 세계 최초로 개발하는 등 초정밀 금형 기술을 선도했다.최근 ‘ER몰드’ ‘압축성형금형(ICM)’ 등 기술을 세계 최초로 개발·상용화하면서 전 세계 자동차와 가전업계의 제조 원가를 절감하고 디자인 혁신에 크게 기여했다는 평가를 받고 있다. ER몰드란 금형 내 전기히터를 이용한 급열·급랭 플라스틱 성형 기술로, 플라스틱이 이 금형을 통해 굳어지면 자동으로 높은 광택을 낸다.
레이몰드 관계자는 “금형의 온도를 높이는 등 특정 조건에서 플라스틱을 성형하면 나중에 도장 작업을 하지 않아도 고광택이 난다”고 말했다. 이 기술은 공정을 단축시켜 제품 생산성도 대폭 높였다. 10㎝ 두께에서 0.3㎜의 얇은 두께까지 균일한 품질로 플라스틱 성형이 가능하도록 한 ICM 기술 역시 이 회사가 개발한 미세 가공 신기술이다.
글로벌 완성차, 가전업계 주문 잇달아
국내 완성차업계를 비롯해 제너럴모터스(GM) 스텔란티스(옛 크라이슬러, 푸조) 폭스바겐은 이 회사의 금형 기술을 접목한 중앙 컨트롤 패널, 무드등, 공조기 등을 자동차에 장착하고 있다. 조작 버튼이 모여 있는 중앙 컨트롤 패널은 자동차 내부의 얼굴과도 같아 고급 디자인이 적용된다. 삼성전자, LG전자 등도 TV 모니터 사운드바 등 외관에 이 회사의 금형 기술을 접목하고 있다.보통 플라스틱 금형은 값싼 제조 원가를 무기로 한 중국 업체가 강세를 보이지만 초정밀 플라스틱 금형 분야는 이 회사의 기술 장벽을 넘지 못하고 있다. 이 회사의 지난해 매출은 290억원으로, 80%가 전 세계 15개국 수출 물량에서 나왔다.
하 대표는 고교 1학년 때 아버지를 여의면서 가정 형편상 학업과 양복점 장사를 병행해야 하는 등 어려운 학창 시절을 보냈다. 정밀 기술에 대한 목마름으로 대학 시절 금형 기술을 배워 대한전선 LG전자 등에서 근무하다 1985년 전문 금형기업을 설립했다. 그가 기술 인력 양성을 위해 그동안 2억원의 장학금을 후원한 것도 이런 경험이 계기가 됐다. 하 대표는 “제품 디자인이 점차 중요해지고 탄소 배출 규제가 강화되면서 ‘친환경 무도장’ 금형 기술에 대한 수요도 커지고 있다”며 “앞으로 5년 내 매출 500억원 달성이 목표”라고 말했다.
안대규 기자 powerzanic@hankyung.com