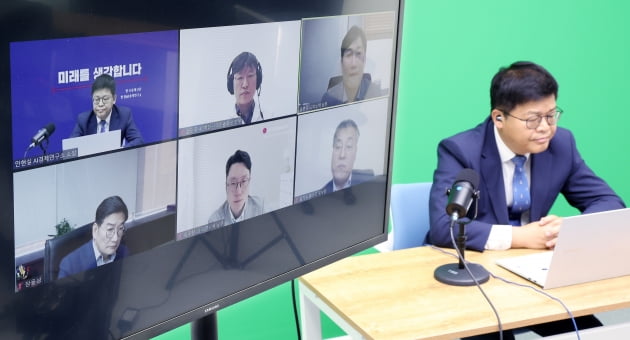
“전기전자 부품 업계가 과거엔 표준 부품 하나를 대량생산했다면, 이젠 고객사별 요구에 맞춰 다양한 부품을 소량 생산해야 합니다. 고객 요구를 미리 예측하기 어렵기 때문에 부품 개발 과정을 단축할 수 있는 ‘디지털 트윈(Digital Twin)’이 필수적인 이유입니다.”
김민규 LG이노텍 상무는 지난 9일 한국경제 AI미래포럼이 ‘인더스트리얼 인공지능(AI) 우리가 한다’라는 주제로 개최한 웨비나에서 이 같이 말했다. 이날 웨비나에 참가한 기업인들은 산업현장에서 AI가 어떻게 활용되고 있는지 사례를 공유했다.
김 상무는 완성품보다 먼저 개발을 시작해야 하는 부품 산업의 특성 때문에 AI의 활용이 중요하다고 강조했다. 통상적으로 휴대폰이나 자동차 등 완성품에 들어가는 부품은 완성제품이 나오기 최소 3년 전부터 개발을 시작해야 한다. 김 상무는 “고객의 요구와 시장 개화 시기를 예측해야 하지만, 다품종 소량 생산 시대엔 이 예측이 어렵다”고 지적했다.
디지털 트윈을 활용하면, 이 예측에 차질이 생기더라도 개발 기간을 줄일 수 있다. 디지털 트윈이란, 현실 세계의 기계나 장비, 사물 등을 컴퓨터 속 가상세계에 쌍둥이처럼 구현하는 시스템이다. 실제 제품을 만들기 전 가상세계에서 모의시험을 펼치고, 발생할 수 있는 문제점을 미리 파악해 해결하는 것이다. 김 상무는 “현실 세계의 행위를 30% 이상 단축할 수 있어야 개발기간을 줄이고, 사업이 생존할 수 있다”고 강조했다.
건설 현장에서도 AI가 적용되고 있다. 김판영 HD현대사이트솔루션 전무는 휠로더 등 중장비에 사용되는 기술을 소개했다. 휠로더 앞 부분의 커다란 버켓은 운전자의 시야를 가리는데, 장비 주변의 카메라로 주변 영상을 촬영한 후 AI로 조합하면 운전자 입장에선 버켓이 마치 없는 것처럼 시야가 확보된다. 일종의 ‘투명 버켓’으로 건설현장의 안전을 확보하는 기술이다.
장기적으로는 건설 장비가 ‘자동화(Automation)’에서 ‘자율화(Autonomous)’ 장비까지 발전해야 한다는 지적도 나왔다. 김 전무는 “운전자를 돕는 일부 자동화된 장비가 앞으론 운전자 없이 아예 모든 것을 자율적으로 판단해 실행하는 장비가 돼야 한다”고 했다. 자동화 장비는 관리자가 지정해준 고장 코드를 진단하는 수준이라면, 자율화 장비는 고장이 무엇인지 스스로 판단하고, 더 나아가 고장을 예측하리란 의미다. 김 상무는 “고장 진단 솔루션뿐 아니라. 최소한의 에너지로 최대 작업을 돕는 ‘AI 파워모드’, 주변 카메라로 장애물과 사람을 인식해 건설현장 안정성을 높이는 ‘AI 가드’ 기능 등을 개발하고 있다”고 덧붙였다.
AI를 도입하기 특히 어려운 산업도 있다. 김기수 포스코 부사장은 “AI를 활용하려면 데이터 수집이 필수적인데, 철강 산업의 경우 고로의 내부 온도가 매우 높아 데이터 측정이 어렵다”며 “AI가 한번 오류를 일으키면 전체 설비의 큰 사고로 이어질 수도 있다”고 했다. 그럼에도 포스코는 AI 도입으로 낭비되는 쇳물을 줄여 생산성을 높이는데 성공했다. 냉각기 등으로 보호한 AI카메라가 쇳물을 촬영하고, 불순물을 자동으로 감지해 제거하는 식이다.
최예린 기자 rambutan@hankyung.com